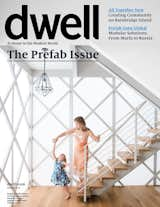
Control over timeline, control over budget, control over the site. But how many projects are built without at least one maddening, last-second complication? Judging from those glimpsed in the December 2017 issue, not many.
Long before the foundation was poured for Anthrazit House in Santa Barbara, Architects Magnus and EcoSteel explored how to protect the structure from wildfires like the one that destroyed the previous home on the property. The result combines concrete and glass with a fire-resistant prefabricated steel superstructure, an exterior skin of insulated metal panels, and a steel roof. Since most homes in the area are framed in wood, the architects spent additional time locating a steel erection team capable of assembling the structure. Installing the steel-and-glass stair alone required a five-ton hoist.
David Packer and Linda Gaunt’s Breezehouse in New York’s Hudson Valley was shipped cross-country and installed as painlessly as can be imagined. Yet significant site work needed to be done after Blu Homes, the fabricator, exited the picture. Packer made the decision to tweak the layout, and even added a site-built "connector" to unite the property’s three separate prefab buildings. Now the couple has a home that is tailored to their needs, and they had a hand in building it.An unusual—and gratifying—element of this issue is our cover story, which features the Venice, California, home of designer Jennifer Siegal. Proving that Siegal is rightfully one of the leaders of prefab’s possibilities, the story exemplifies how her mind and home are constantly evolving, shifting to include those possibilities. This is the second time this residence has appeared—the first, in 2007, highlighted how Siegal creatively added to the 1920s bungalow on the site with a 200-square-foot truck trailer. A freestanding, two-story studio followed. We now return to see the property’s latest incarnation. The truck trailer is gone, and in its place are three stacked prefab modules, something Siegal calls "vertical urban infill."Prefab construction is a complex topic, and one we’re still wrapping our heads around. The method upholds the virtues of consistency, speed, and customization, as well as material resourcefulness.
It would seem logical that financial resourcefulness would follow, but, as is proven often, this is not always the case.
We recently met with New York architect Jeffrey McKean to discuss the pros and cons of prefab, and the factors that might be preventing it from a more mass application. He seemed to think the main challenges stem from the fact that prefab presents a new paradigm that simply isn’t familiar to traditional construction firms. Our takeaway is that prefab is standardized at the production level, but it has a ways to go at the construction level. As the stories in this month’s issue show, building methods vary from one prefab design to another, and for workers used to conventional methods of building, it can be seen as a challenge to their skill set, or as a new system that will make their jobs obsolete. That couldn’t be further from the truth. As a way to work around this, McKean, who has a background in carpentry, has started to bring contractors in only after he does the initial setup of the envelope himself. This allows the contractors to install the building systems without having to go through the hurdle of the initial setup, which McKean says is what frustrates them.
The Grow Community story underscores the potential for prefab on a larger scale. Although, in the end, modular construction didn’t work for that project, the story should be considered an attempt by passionate believers in sustainable solutions. Despite the obstacles, the project is an important addition to the mix, as it highlights a case study that perhaps inspires more questions than answers.
We call upon the construction industry, as well as our elected officials, to catch up and come aboard. Let’s embrace the power of prefab and champion technology. "As digital tools become more powerful, cheaper, and more common, the potential to control the building process will allow for more flexibility and attention to creative results," Geoffrey Warner of Alchemy Architects said to us in a recent interview. "The more that we can take the element of human error out of the construction equation, the more we can use our talents to be really productive."
We are reminded that architecture is part of a political system—one intertwined with developers, business demands, community members, building codes, and so on—and one that can’t easily be overturned with a kit-of-parts solution.
More Prefab Home Articles You May Like
Published
Last Updated
Topics
Prefab HomesStay up to Date on the Latest in Prefab Homes
From cozy cottages to large family houses, see how prefab continues to redefine the future of construction, building, and design.