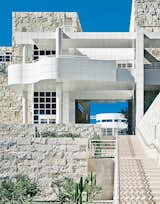
Richard Meier on Designing With Marble
Although you had worked with stone before, after your design for the Getty Center was complete, you really became known for working with the material. Tell us about your experience learning about travertine at the Bagni di Tivoli quarry in Italy.
When we were chosen as architects for the Getty Center, we had to go through a whole conditional use permit to build on the site, and one of the conditions was that the buildings couldn’t be white. I thought, That’s fine, the Getty is an institution that’s going to be around for a long time; we wanted to use a material that had a sense of permanence, so we wanted to look at stone. And we got samples of stone from just about every quarry in world in our model shop in Los Angeles. We had enough stone to build most buildings, in samples, and I kept looking at stone, and at some point someone said, What about travertine? I said, Nah, I know what travertine looks like, Lincoln Center is made out of travertine, I want something that has more texture. [The Italian stone artisan] Carlo Mariotti said to me, "Well, we could get some texture in travertine. So he invented this guillotine that sort of cut the stone. In the beginning we got a lot of gravel; it didn’t work and then after quite a lot of experimentation we got it to work and to cut the stone in the rough finish that you see in the building today. And because of the process, the pieces on the conveyor belt were about eight inches wide, so after it was cut and cleft, then we cut it so the middle piece, which was a by product of the process, was then used as paving, so there was no waste of material. And we got the stone for the facade that we wanted.
Can you explain the "guillotine" process of cutting the travertine blocks that results in that rough, textured finish we see at the Getty?
Well the guillotine was a huge machine, and blocks of stone would be put on a conveyor belt, the belt would take them and the guillotine would come down and cut the stone. And the blocks of the cut stone were about a little over a foot wide, and that would go through a saw to cut it so that you got both sides as a façade stone, and the middle piece that was cut out is the paving stone.
So the roughness of the outside, was that just the roughness of the stone?
No, well, it’s the natural surface of the stone as cut by the guillotine.
You used travertine again for the Ara Pacis museum in Rome.
How does it differ from what you did at the Getty, and how does it interact with the marble on the Ara Pacis itself?
With the design of the Ara Pacis, which was done after the design of the Getty, I figured, If you’re working in Rome, you should use stone from Rome. There’s travertine everywhere in Rome, but not like what we have at the Ara Pacis. It’s from the same quarry as the Getty’s.
Did you use the same effect?
Yes. But the size of the pieces are different; they’re not the same as the stone at the Getty. They’re slightly smaller.
Regarding the art piece itself, the Ara Pacis, did you consider its material when you created the wall and the surrounding for it?
Yes.
How do the two stones interact?
The space where the Ara Pacis is located is glass. The roof is also glass, so it’s like a glass enclosure. And the walls for the Ara Pacis are for the most part not in the space where the Ara Pacis is, so there’s no direct connection.
Even so, you must have considered greatly the material of the work itself.
Yes.
How do you feel that they interact, even indirectly?
I think it works beautifully because the Ara Pacis itself is much whiter than the travertine.
We’ve been contemplating the color of the Getty for a long, long time. Perhaps it was fortuitous that the coding wouldn’t allow for a bright white building.
At first, I thought I shouldn’t take it personally, but it’s an appropriate material for the Getty. As I said, the Getty is an institution of permanence and longevity, and the stone reflects that.
Why was granite cladding the best material to use for the Des Moines Art Center addition?
The Des Moines Art Center, the original building was designed by Eliel Saarinen, and then there’s an addition in the 1960s by I.M. Pei, and this is like a third addition, so the building wasn’t going to mimic either of the previous two parts of it, but it had to connect to it. And it seemed to me it had to in some way harmonize with the existing buildings both in terms of its materials as well as in terms of the scale.
Going a little bit smaller to the residential scale, do you feel like you have more freedom to work with the material on a scale such as this?
No, every project is different. This house happens to be on the water overlooking the water, and you step outside onto the deck, you want to use stone, it’s a natural material. That also then starts on the inside—the floors are stone—and continues to the outside.
What’s the most difficult stone to work with?
I don’t thing there’s one stone that’s more difficult than any other. I think that for most part when we use it in the way we did at the Getty, the water drains behind the stone, so that the joints are not mortar joints as they are here, with a kind of monolithic surface, but you can read each piece of stone because of the void at the joint, which is a clearer reading of the stone. By draining the water behind it, there’s no staining, and the air pollution doesn’t leave a residue on the surface. The smog in Los Angeles is horrific, so you don’t want that on your building.
What are you working on now, stone or otherwise?
We have work under construction in Tokyo, in Tawian, a project in Mexico City was supposed to start but it’s been delayed, so we have work all around under construction. There’s housing in Newark, New Jersey, we have work everywhere except in New York! Newark is residential, it’s teachers’ housing, it’s quite a large project under construction. We’re doing a hotel in Korea, which is under construction, also in Taiwan, those buildings will start soon, residential towers. Stone not in terms of the facade but certainly in terms of the flooring. In Mexico we’re doing another residential and commercial building, and a hotel. And we’re also doing a two residential buildings in Bogota. And in Miami.
Typically your residential commissions are larger scale. Is this to say you won’t be doing any more single-family residences?
You know, I try to discourage people from doing single-family houses, because it’s a lot of work, it takes longer, you go to buy a house and you know what you’re getting, it’s less expensive and you can move in right away, you don’t have to go through the process. So I try to discourage people but if they’re persistent, I say, OK, we’ll do it.
Published
Last Updated
Get the Dwell Newsletter
Be the first to see our latest home tours, design news, and more.