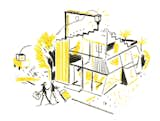
Will 3D Printing Solve the Affordable Housing Crisis?
Owning one’s own house—a dream of human beings ever since Cro-Magnons looked out of their caves at the retreating glaciers—has been sometimes more, sometimes less affordable. Currently, we’re in one of the less affordable phases. With construction accounting for almost 60 percent of the cost of a new single-family home, measures that reduce labor and simplify material needs may make the dream more accessible for many.
Cue the 3D-printing evangelists. The 2010s have been ringing with the hosannas of houses extruded from a 3D printer in hours, sometimes many of them per day. The options seem limitless, with made-to-order versions in concrete, like Icon’s tiny house in Austin; ABS plastic and carbon fiber, like Branch Technology’s prototype home in Chattanooga; and recycled materials, like Chinese manufacturer WinSun’s five-story apartment building in Suzhou. By simplifying construction, we’re told, 3D printing can provide affordable shelter to everyone from the working poor to refugees.
Except it hasn’t. To date, 3D printing has built only a small slice of new housing. And while printers have been put to use fabricating prosthetic limbs for refugees, we’ve seen no reports yet of displaced people living in mass-produced 3D pods.
One reason for the delay is that the technology and processes are still evolving, which means that 3D-printing a house requires considerable human capital. Icon’s adorable hut required a handmade roof. WinSun’s building was 3D-printed in pieces in a lab, transported to the worksite, and then assembled by hand. In nearly all the major projects so far, humans have had to be involved in everything from putting rebar into the 3D-printed walls to installing plumbing pipes and electrical wires in the 3D-printed conduits. That’s good news for hard-hat workers. But what happens when the technology improves?
It’s a question that some major players in the industry haven’t fully confronted. The National Association of Home Builders, a trade association with more than 140,000 members, has not yet gathered experts to look into 3D printing’s impact. "Maybe five, ten, fifteen years from now, we’ll be at that point where 3D printing gets traction," says Craig Drumheller, who leads the group’s Construction Codes and Standards department. Still, even without an official report, he can imagine what the effect might be on tradespeople: "At the end of the day, the builders are looking for the most cost-effective way to build the product for the consumer. And if they can do it with three people and a giant 3D printer, then that’s the direction they’re going to go in."
• According to the Boston Consulting Group, as of the beginning of 2018, fewer than 40 large-scale projects and prototypes globally had been built using 3D-printing.
• But the tools and processes are progressing rapidly. Dubai is aiming for a quarter of its new buildings to be based on 3D-printing technology by 2030.
Published
Topics
Home TechGet the Dwell Newsletter
Be the first to see our latest home tours, design news, and more.